CASE STUDIES
Brother UK
Brother UK increased OEE from 74% to 83% in 3 years following implementation of Intouch MES
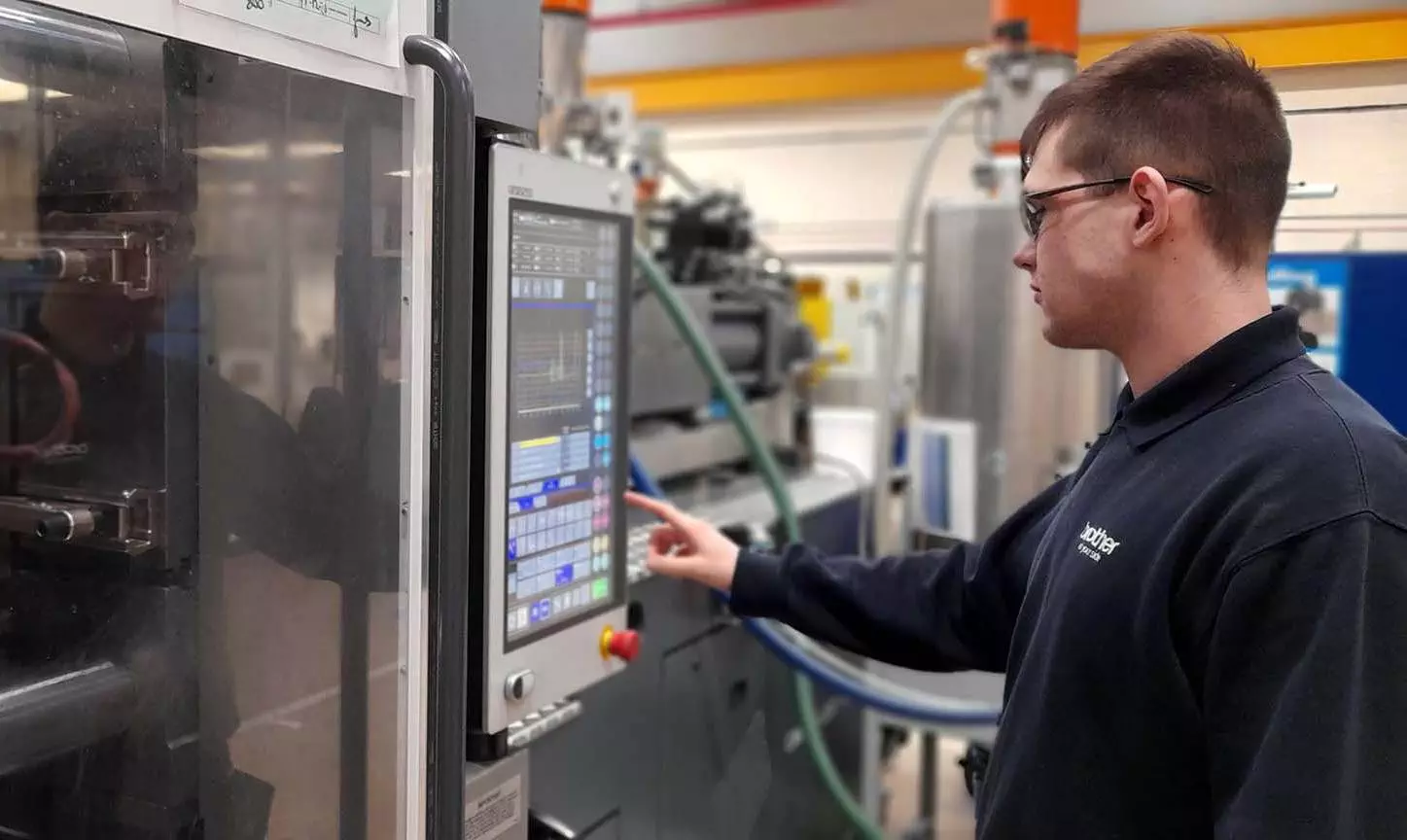
Brother UK is a recognised, household brand with a very long history. Celebrating over 100 years, the first European base was established in Ireland in 1958. In 1968 they took over the Jones Sewing Machine factory in Manchester, and to this day they still produce sewing machines.
Brother have a reputation for being innovators, introducing the first dot matrix printer in 1971, the worlds thinnest self-contained printer in 2004 and the first desktop scanner with built-in wireless connectivity.
At their Wrexham location, Brother has 13 moulding machines ranging from 40 to 550 tonnes, with the capability to produce parts from under 1 gram to 2.5 kilograms. Their diverse range includes precise technical mouldings for the electronics, automotive, and medical industries. They are an unusual set-up being an in-house moulder and also a third party trade moulder. They are also a zero waste-to-landfill site and a carbon-neutral site. They are very focussed on energy monitoring, sustainability and reduction of waste, with many of their machines now electric.
Typical customers include those requiring precise, technical mouldings, such as in the electronics, automotive, and medical industries. They have also recently taken on new business from the inkjet printer and business machines sectors.
The Challenge
As part of a company-wide Industry 4.0 initiative, they sought to enhance production efficiency, reduce waste, and improve data access across various departments.
The company were facing significant delays in production reporting and scheduling, which were primarily handled through spreadsheets. Prior to implementing an MES (Manufacturing Execution System), the time taken to generate Overall Equipment Effectiveness (OEE) data and production reports was proving inefficient. Their OEE stood at 74%, and scheduling processes consumed a substantial amount of labour hours.
There was also a requirement to reduce the response time to production issues, as feedback loops were delayed, leading to slower corrective actions on the shop floor.
Identifying a solution
After evaluating several MES systems, the company selected the Intouch production monitoring system due to its competitive pricing, user-friendly interface, and ease of installation. The system was part of a larger initiative that also included installing digital computer maintenance and health and safety management systems.
Intouch’s real-time data analysis, particularly the immediate feedback on production statuses, was crucial in enabling quicker responses to machine-related issues and improving labour efficiency.
Benefits to Brother UK
Key benefits realised from the implementation of the Intouch system include:
- OEE Improvement: The company saw an increase in OEE from 74% to 83% within 12 months of using the system
- Time Savings: Intouch system enabled Brother to save 400 hours in scheduling time and 150 hours in generating production reports over 12 months
- Labour Efficiency: Labour efficiency increased by 15%, thanks to better visibility of operator utilisation, enabling quicker adjustments to labour allocation
- User Engagement: The system’s user-friendly interface ensured high adoption rates, with 90% of the system’s functionalities being actively utilised by departments, from the shop floor to quality control
- Feedback response: The Intouch system provides real time allowing for faster and more efficient response times to problems
- The reporting function: The reporting and dashboards helps target resources to improve the right areas, following the 80/20 rule where 20% of parts account for 80% of problems
In addition to measurable gains, the transparency and accessibility of production data fostered a shift from spreadsheet-based workflows to collaborative, real-time monitoring of the shop floor via live dashboards.
Meetings now leverage this data, promoting alignment on priorities and schedules across departments.
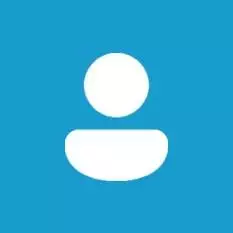
'We saw the Intouch system in action at one of your other customers, and really liked it. It was very user-friendly, and offered all the functionality we were looking for, at a very attractive price – much better than many competitors. We found installation very easy, and extremely happy with the results we have achieved.'
Neil Lloyd Richards, Moulding Manager
Outcomes
Neil said, “The system’s impact exceeded expectations”. The clear visual feedback provided by Intouch, such as status displays for machines and cycle time alerts, allowed the company to resolve production issues more quickly. In particular, the ability to monitor and adjust scheduling based on real-time data resulted in a drastic reduction of manual work, enabling scheduling staff to focus on other responsibilities.
Additionally, the system fostered healthy competition between shifts as performance metrics were easily accessible and shared.
The company’s commitment to reducing waste and energy consumption was also bolstered by Intouch, as its electric moulding machines were better managed through the system’s feedback and data analysis capabilities.
Conclusions
By implementing the Intouch Production Monitoring system, Brother has significantly improved its operational efficiency, saving hundreds of labour hours and boosting production performance metrics.
The system’s ease of use and real-time reporting allowed for quicker responses to production issues, improved labour utilisation, and better scheduling efficiency. Overall, the system proved instrumental in supporting the company’s broader Industry 4.0 goals, setting a foundation for continued digital transformation.
Ready to increase your productivity?
We would love to hear from you. Call, email or use the contact form and we’ll get right back to you.
Headquarters
Intouch Monitoring Ltd
The Bull Pens, Tithe Farm
Moulton Road, Holcot
Northamptonshire
NN6 9SH