CASE STUDIES
Progressive Plastics Inc
Custom injection moulding company Progressive Plastics use Intouch Production Monitoring to gain greater focus on their manufacturing capabilities
Progressive Plastics was founded in 2004 and is a full-service injection moulder. They supply products for industries such as Military, Aerospace, Office, Plumbing, Construction, Filtration, and Marine just to name a few. They have a wide variety of thermoplastic machine sizes, and the engineering staff work closely with customers to bring a concept from design to finished mould and part. The company is agile and able to fulfil customer demand no matter how difficult the task.
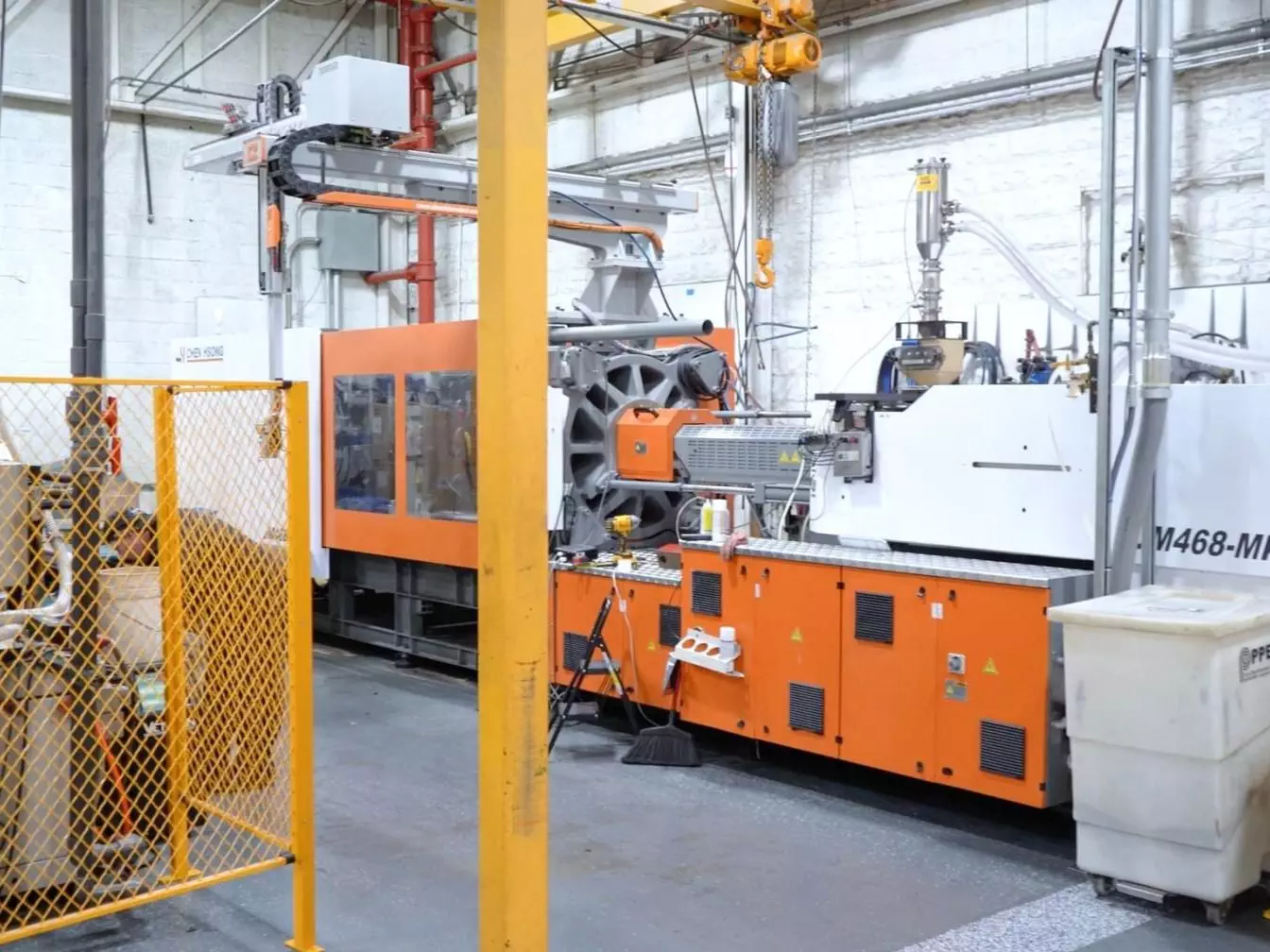
The world of plastic injection moulding is ever advancing and offers many opportunities for companies and inventors to take advantage of creating or replacing parts that are more economically viable when made of plastics rather than other heavier or more expensive materials. Based in Elwood in Indiana, the company has garnered a reputation for excellent customer service and maintains a focus on continuous improvement within their manufacturing lines.
As with many growing organisations the requirement for automation is often linked with the desire to lower costs and accelerate production without sacrificing quality. Events of the last 5 years are testament to the desire to retain business continuity in the face of adversity and investing in automation future proofs organisations against times when human intervention may become limited.
Watch our case study video:
The requirement for a monitoring solution
David Harbit, Co-founder of Progressive Plastics and a seasoned Process Engineer with over 40 years of industry experience, has remained deeply engaged in the company’s day-to-day operations. While he had previously relied on production monitoring software to oversee equipment like moulding machines and conveyor systems, David recognised a critical gap in aligning the production floor with supply and demand.
“Our 13 injection moulding machines range from 60 tons to 770 tons, with shot capacities between 2.5 ounces and 88 ounces,” David explains. “It’s essential to know if we’re at risk of falling behind on output targets. We needed a system to integrate scheduling, display cycle-time profiles, and generate automated reports.”
This realization led David to discover Intouch Monitoring’s Manufacturing Execution System (MES)—a cost-effective, real-time production monitoring platform with a fully integrated scheduling board for dynamic planning. “What stood out was Intouch Monitoring’s extensive experience working with injection moulding equipment,” he adds.
The limitations of their previous system were clear. It provided only basic data on machine availability and required physical checks to access cycle times and shot counts. “Everything was manual,” David recalls. “We had to load data into a program and would often only find out after the fact if issues had occurred.”
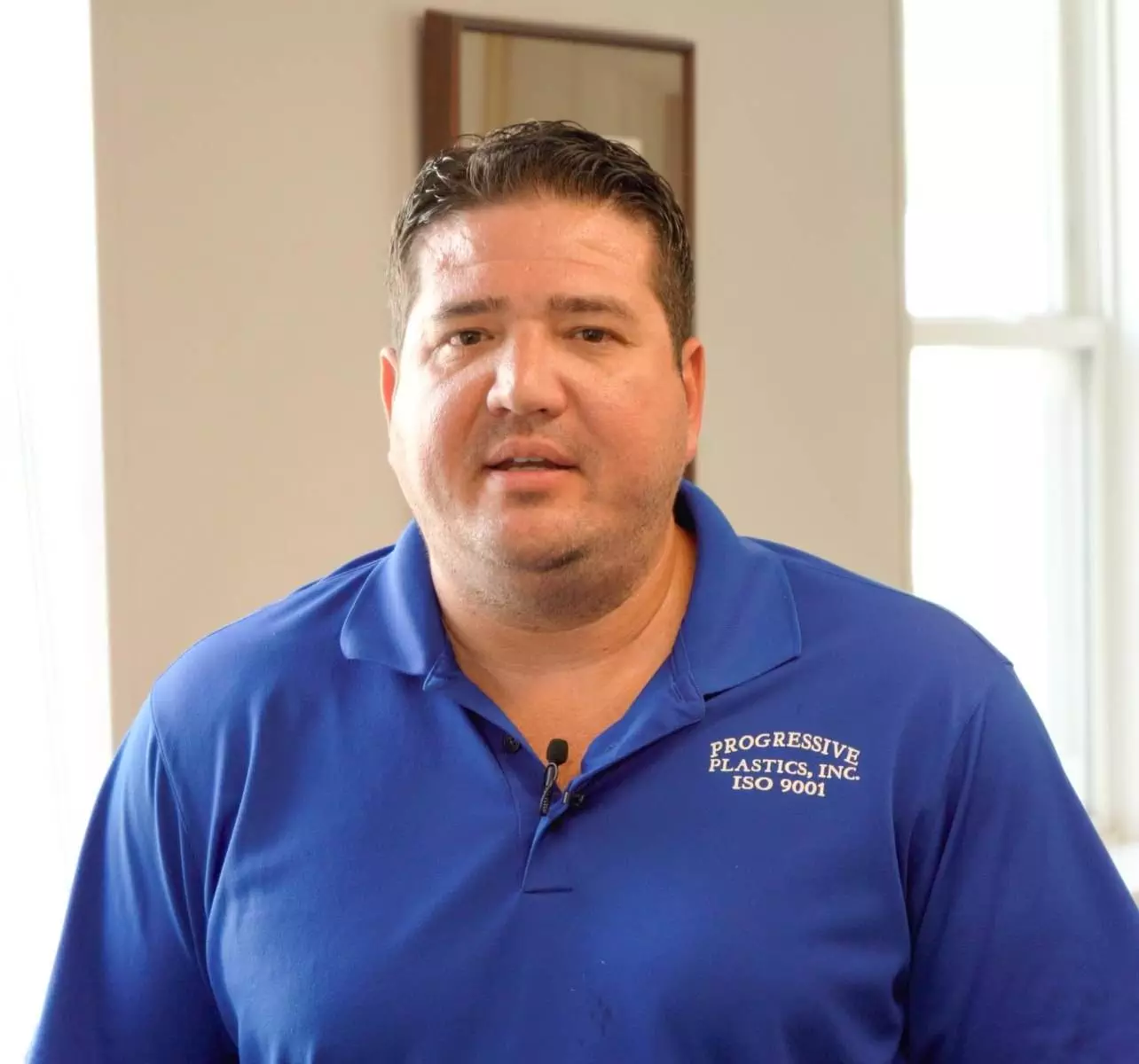
'To track cycle times, shot counts, or other parameters, we had to visit the machines directly. We wouldn’t know until the end of a shift if something was running out of spec. Plus, planning product runs was challenging without real-time visibility into tool availability.'
Matt Lemerick, Quality Manager
Driven by the need for a smarter solution, David and Matt began their search for a system that combined real-time monitoring with scheduling capabilities. After evaluating functionality, pricing, and customer support, they chose to trial Intouch Monitoring. They connected the system to a few of their injection moulding presses, setting the stage for a transformative shift in operations.
The Solution
The Intouch solution was implemented and fully operational within just a few days. Connecting the machines was a straightforward process, with each unit hard-wired to Intouch Monitoring’s XTX box and integrated into the factory network.
Intouch Monitoring managed the entire project, working closely with Progressive Plastics to define clear objectives and goals. The system was quickly up and running, accessible from any device with a web browser.
Crucially, the production schedule was now synced with the shop floor, enabling greater operational agility and providing early warnings of potential bottlenecks. This alignment offered Progressive Plastics a significant boost in efficiency and control over their manufacturing processes.
The Benefits
“Intouch Monitoring has given us real-time visibility into our production area, allowing us to address issues immediately and significantly improve our efficiency,” says David Harbit.
As part of the implementation, David and Matt installed a large screen monitor on the production floor. This display provides all operational staff with a clear overview of current product runs, along with real-time visibility of uptimes and cycle times. The days of waiting until the end of a shift to assess progress are gone. Adjustments can now be made instantly, ensuring proactive improvements to output performance.
“Our efficiency has seen a significant boost since adopting Intouch,” David explains. “We can quickly assess current machine utilization and gauge our ability to meet future
demands. This insight not only optimizes daily operations but also informs our long-term strategy, helping us determine when additional manufacturing equipment might be necessary to handle rising demand.”
Working with Intouch
“Intouch has been incredibly supportive, both during the installation and beyond. We’re constantly learning, and their customer support team is always available to answer questions and provide guidance,” says David Harbit.
Progressive Plastics is in the early stages of integrating the Intouch Monitoring platform into their daily operations. As they continue their journey toward operational excellence, they anticipate uncovering even more benefits from the system.
“My advice is to take full advantage of the diverse tools Intouch offers,” David adds. “The platform equips us to make informed business decisions, helping to drive the company’s growth and ensuring a more efficient future.”
Intouch Monitoring: Real-Time Solutions for Modern Manufacturing
Intouch Monitoring offers a comprehensive, cost-effective, and user-friendly production monitoring system designed to address critical challenges in manufacturing. Tailored to meet customer needs, it empowers businesses with complete control and visibility over their operations.
Key Benefits:
- Real-Time Access: View live production data anytime, anywhere, on any device.
- Affordable for All: Scalable solutions for businesses of any size or industry.
- Proven Expertise: Backed by over 25 years of experience and a dedicated, hands-on support team.
- Global Trust: Trusted by more than 300 businesses worldwide.
- Comprehensive Features: Includes monitoring, scheduling, reporting, a mobile app, and API-based add-ons.
- Quick Implementation: Easy setup in hours, with measurable results within days.
- Risk-Free Trial: A free 60-day trial for critical machines to demonstrate rapid ROI.
Intouch Monitoring delivers complete production process visibility with accurate, real-time information and instant alerts, accessible across desktops, tablets, and smartphones. With headquarters in England, United Kingdom, and a global support network, Intouch Monitoring is a trusted partner for manufacturers worldwide.
Ready to increase your productivity?
We would love to hear from you. Call, email or use the contact form and we’ll get right back to you.
Headquarters
Intouch Monitoring Ltd
The Bull Pens, Tithe Farm
Moulton Road, Holcot
Northamptonshire
NN6 9SH